過去の仕事で面白いのをご紹介します

少しずつ内容を増やしていきますが、まだまだ工事中です。
弊社の最近の仕事の中で特に面白い仕事を紹介させていただきます。
「PLC計装システムとPLC通信」は9台のPLC計装CPUをMELSECNET/Hで接続し集中監視を可能とした例です。
「PLC二重化システム」はシーケンサCPUおよび電源、タッチパネル、IO用直流電源などを二重化し、自動弁操作スイッチなどを徹底的に削除した例を載せました。
「無線テレメータ」は埋設した光ファイバーケーブルの品質低下により、多重伝送システムに支障を来した対応策として納入しました。ほとんど新規工事は必要なく、ちょっとした盤改造で可能です。免許も必要なく安定した通信が出来ています。
上位DCSの端末としてPLC−NETを使用して、安価にシステムを構築した例を「上位DCSとPLC−NET接続」に載せました。DCSが苦手な高速処理もシーケンサで分担して処理することも可能ですので、ますますこの形での処理が増えるのではと思っています。
下水や農水処理に用いる曝気装置に溶存酸素(DO)制御を用いた制御システム[DO制御を用いた曝気装置」をご紹介します。操作及び管理は全て タッチパネル画面のみです
PLC-NETで多数のPLCの情報を吸い上げ、タッチパネルマルチリンクシステムで総計47台のタッチパネルにデータ表示をする監視システムの例を「PLC-NETとタッチパネルマルチリンク」に載せました。
ワンループコントローラを使用した「非線形比例制御」を具体的な説明を入れてご紹介しています。
製糖工場に関係するものとして精製糖工場の「真空結晶缶自動制御」です。
この精製糖工場の「真空結晶缶自動制御」は既設のリプレースでしたが、これを汎用化した汎用砂糖結晶缶制御」の基本的な部分を作りました。PLC計装、SCADAの組み合わせで面白いものが出来たと思いますが、ここの仕事例には該当しないので別サイトとして独立しました。。 
9台のPLC計装CPUをMELSECNET/Hで接続し、パソコンによる集中監視を可能とするシステムを構築しました。制御の詳細が決まってから試運転完了までわずか6ヶ月と超突貫の仕事でしたが、社内標準化されたソフトで大幅にソフト作成時間を短縮でき、かつバグの発生が抑えられ、お客様の要求納期に間に合わせることが出来ました。
PLCソフトとともにTP画面も 、単独調節計、カスケード調節計(トラッキング処理付き)、バッチ処理調節計、比率制御調節計、指示警報計、比率設定器、出力操作器などが標準化されています。また、バッチ処理調節計では出力外部帰還を設け、調節開始MV値をバッチ内容により変更出来るようにして、スムーズな調節開始を可能としました。
動力機器、自動弁なども全てタッチパネル操作になっています。当然これらのPLCソフト、TP画面も標準化されています。
今回各制御盤にバッチシーケンスがかなりの量あったのですが、PLC計装を使用することによりスムーズに両者の融合が出来ました。また、バッチシーケンスも標準化されたソフトを使用しましたので、EXCEL表を整理することで動力機器動作や自動弁開閉タイミングの変更が可能で、試運転時の変更に柔軟に対応出来ました。
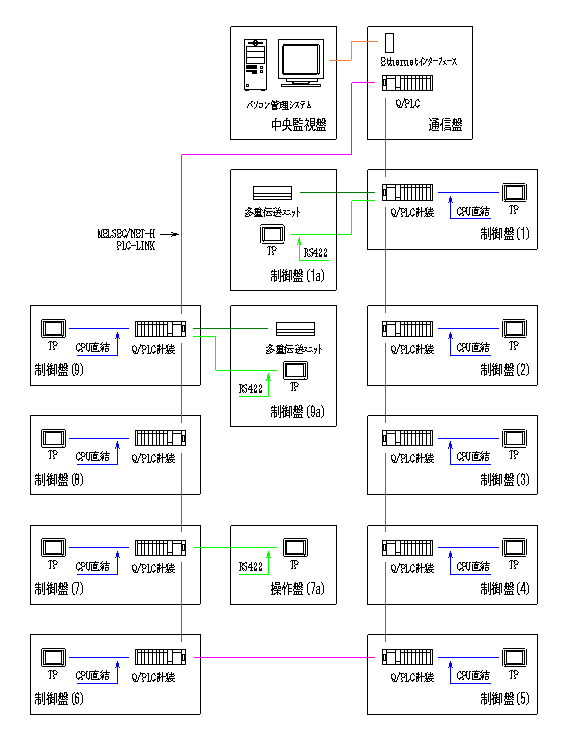
この様なシステムは個々のPLCソフト以上に全体を見据えたNET割付が重要になります。1台のPLCのNET割付を間違えただけで全体の割付変更となります。NETUからNET/Hになって大幅に割り付け可能エリアが広がりましたが、まだまだ不足という感じがします。
このシステムとは別ですが、調節ループ数の少ない(8ループ以下)場合、PLC計装CPUを使用せずに一般CPUのPID演算を使用したバッチ制御の標準化ソフトも作りました。ソフトは若干複雑になり、バッチ処理の方法がPLC計装とは別になりましたが、うまく動作しています。価格的にはPLC計装CPUに比べかなりのコストダウンになります。

実に20数年前、私が関連した浄水場ろ過池設備の更新工事がありました。盤構成を変え、配置上も狭くなり、故障時の対応も考えPLC二重化システムを導入することにしました。
PLC二重化システムとは
今回使用した三菱電機Qシリーズの二重化システムはCPU、電源、ベースを含めた基本システムを二重化することにより、制御系で故障が発生した場合でも待機系に制御が切り換わり、システムの継続運転が可能です。前に使用したQ4ARシリーズの場合は同一ベース上に2台のCPUが取り付けられ、完全な二重化とはいえないところもありました。
ただ、IO部分にMELSECNET/HリモートI/Oネットを使用しなくてはいけない点が不満です。ここに別の故障発生要素を作っている感じがします。多分、BUS方式を開発されているとおもいますが・・・。
システム構成
シーケンサ関係を二重化すると同時に、I/Oや表示灯に使用する直流電源を並列二重化し、HMIとして使用するタッチパネルも2台使用し、一般的な故障時に停止することの無いシステムとしました。
主操作スイッチおよび自動弁などの手動操作スイッチも全てタッチパネル操作に変更し、アナログ関係も全てシーケンサ処理(PLC計装ではありませんが)とタッチパネル表示に変更しました。大半がソフト処理ですので、試運転時のお客様の仕様変更要求にも迅速に対応できました。
DCSとの取り合いも中央中継盤までケーブル接続していましたが、CC−LINK(Ver.2)に変更しました。
その結果、スペース的には以前の半分になり、盤内は簡素化され部品点数が減っているので相対的に故障原因は減り、安定した制御が可能となりました。
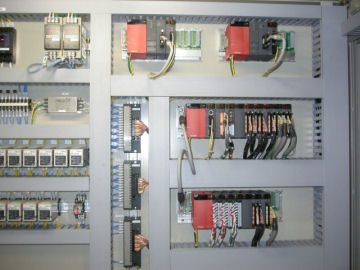
右上に2台のCPUベースがあり、トラッキングケーブルで結ばれています。中段、下段はNET/Hで結ばれたI/O部分です。今回はCC−LINKはリモートI/O部分に組み込みました。アナログを除き、入力はコネクタ−端子台ユニットで、出力もコネクタ−リレーユニットで接続されていています。入力、出力とも外部配線と接続するところは端子台ユニット、リレーユニットをそのまま端子台として使用し、盤組み立ての省力化、省配線化をはかっています。
左上に二重化された直流電源があり、低電圧を検知すると警報を発します。また、瞬時電流、ピーク電流、電圧、寿命等を表示可能です。
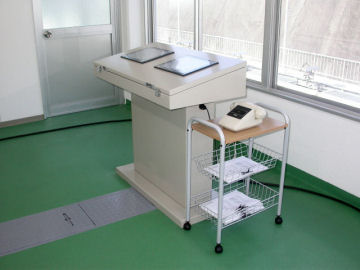
タッチパネルはろ過池に向いた窓前にデスクの形で設置しました。現場を見ながら操作でき、グラフィック画面と現場との対応が理解しやすく好評でした。
タッチパネル画面例
取扱説明書に使用した画面を例に2面ご紹介します。SVGA(800×600)を縮小していますので、縮小していますのでちょっと見にくいですが・・イメージということで。
グラフィック画面では自動弁、動力機器の側にA−Mの表示が出ます。Aは自動ポジション、Mは手動ポジションが選択されていることを示します。自動弁は閉で緑色、開で赤点灯します。動力機器は停止で緑色、運転で赤色、故障で黄色点灯します。
それぞれのシンボルにタッチすると個別の操作ウインドが表示されます。ここの例では流出弁にタッチし、自動選択、自動開の状態を示しています。自動から手動に切り換えたときは自動の状態を保持、その後手動で開閉の操作をするようになります。
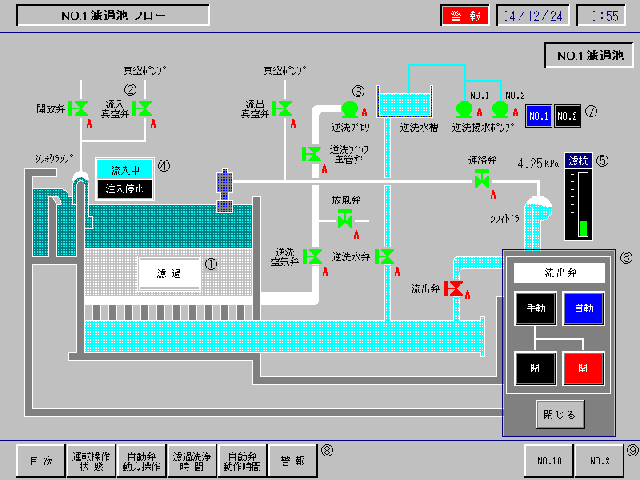
ろ過池個別の操作画面です。各種操作や工程表示、時間設定と経過時間表示、アナログ表示とリアルタイムトレンド等で構成されています。重要な問題点が発生したときは、その詳細をウインド表示して対応しやすくしてあります。
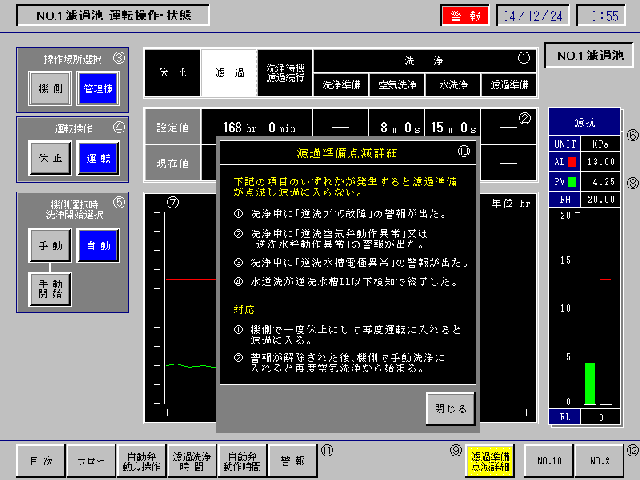

エム・システム技研の無線モデムを使用したテレメータシステムを納入しました。安定した状態で使用できていますので報告致します。
無線テレメータとは
今回使用した機器は429MHz帯特定省電力無線モデムで、免許や資格の必要はありません。周波数チャンネルとして40チャンネルを持ち、単独で使用することも、グループ化して混信妨害に対応して使用することも出来ます。
通信距離は目安として見通しの良い環境(海岸など)で3000m、郊外(田園地帯など)で1200m、山間部(山を越さない)で500m程度とされています。
外部インターフェースはRS−232Cでボーレートは300〜19200bpsですが、今回は4800bpsを使用しました。
データ変調速度は430bpsと遅いため、状況確認は可能ですが制御には使用できません。
周波数別ノイズ状況確認
無線ですからその地域状況、通信距離で安定して使用できるか前もって確認する必要があります。まず、周波数別ノイズ状況を確認します。
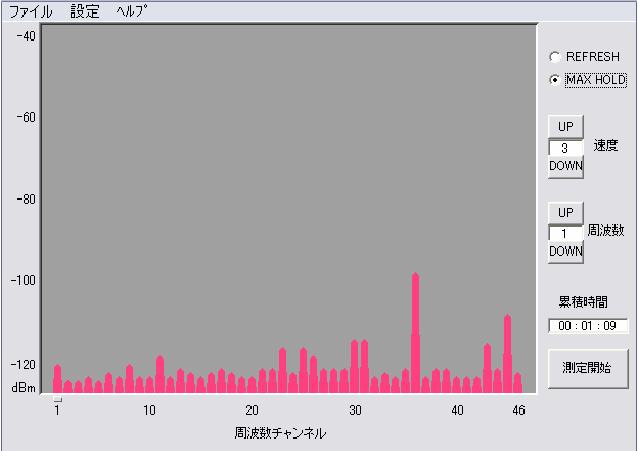
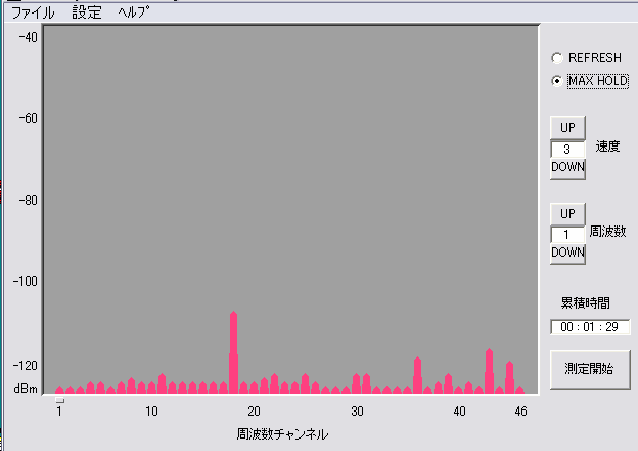
この例の場合、上段図地点ではチャンネルの高い方にノイズが載っていますが、下段地点では18チャンネル以外はノイズが少ない状態で、安定して通信できる可能性大であることが解ります。
これらデータから全ての地点でノイズの少ない周波数チャンネルを選んで使用します。
このテストは無線テレメータの設置場所全てで行います。
受信レベル確認
次に受信レベルの確認をします。この例で受信レベルの−100dBm以下の値は無線テレメーターを床上の横の寝かせた状態のとき、受信レベル−95dBm程度の値は床上で本体を垂直に立てたとき、受信レベル−85dBm程度の値は床上1.5m程度で本体を垂直に立てたときの値です。地上から高いほど受信レベルが向上することが解ります。
データを見ますと突発的な受信エラーの発生も無く、非常に安定した状況です。
BER= 0.0E-2 PWR= -102dBm
BER= 0.5E-2 PWR= -102dBm
BER= 0.5E-2 PWR= -106dBm
BER= 0.0E-2 PWR= -108dBm
BER= 1.0E-0 PWR= -108dBm
BER= 2.5E-2 PWR= -109dBm
BER= 0.0E-2 PWR= -096dBm
BER= 0.0E-2 PWR= -097dBm
BER= 0.0E-2 PWR= -097dBm
BER= 0.0E-2 PWR= -095dBm
BER= 0.0E-2 PWR= -085dBm
BER= 0.0E-2 PWR= -084dBm
BER= 0.0E-2 PWR= -084dBm
BER= 0.0E-2 PWR= -084dBm
BER= 0.0E-2 PWR= -085dBm
BER= 0.0E-2 PWR= -086dBm
BER= 0.0E-2 PWR= -083dBm
BER= 0.0E-2 PWR= -084dBm
BER= 0.0E-2 PWR= -082dBm
BER= 0.0E-2 PWR= -084dBm
BER= 0.0E-2 PWR= -083dBm
BER= 0.0E-2 PWR= -086dBm
受信レベルは−105dBm以上の場合はほとんど問題ありません。ビットエラーは長時間にわたって発生することはなく、突発的なエラーが発生しても、実使用では再送によりエラー訂正が行われるので問題になりません。
注意レベルは受信強度が−105dBm〜−115dBm、危険レベルは−115dBm以下です。
すぐ隣に子局、親局を置いて通信した場合の受信レベルは−45dBm程度です。
実際の施工
実際に使用する場合は1:1のこともありますし、1:Nのこともあります。前述の2項目テストは全地点について行う必要があります。
今回は7チャンネルと27チャンネルの2波で運用しました。2波の場合、何れか電波環境の良好な周波数があれば通信できるため、妨害やマルチパスフェージングに強くなります。逆に周波数を切替えながら受信待機する必要があることから、回線接続時間が若干長くなります。と云うことになっていますが、2波と1波固定チャンネルではテストの結果は殆ど差が見られませんでした。
納入例1は清掃センターの排ガス状況表示盤に使用し、離れた場所の各炉の排ガス状況を無線テレメータで送り道路脇の排ガス状況表示盤で数値表示しています。1:Nの例です。
納入例2は離れた海岸のポンプ運転状況を送信しています。今まで光ファイバーを使用し多重伝送していたのですが、埋設した光ファイバーは水に弱く劣化して誤通信するようになったので、メンテナンス不要な無線テレメータに更新しました。1:1の例ですが、実際は1:Nで設定し子局の増設が何時でも可能なようにしてあります。
何れも安定して通信出来ており、何のメンテナンスも必要としていません。

上位はDCSを使用しても、端末はシーケンサネットを利用する例が増えてきました。シーケンサ端末の方が安価ですし、十分に信頼性もあり、光ファイバーケーブルの引き回しも環境に見合ったケーブルが多種選べますのでそれほど心配する必要もなくなって来ました。
CENTUMとの接続
上位に横河電機のCENTUMを使用し、ハードワイヤー取合とEther取合の2種類でシーケンサと接続しました。ハードワイヤー取合はOMRONのIOリレーを使用して絶縁しています。
この他にゲートウエー取合でRS232Cを使用しての通信も施工例があります。
シーケンサ側は三菱電機製を使用しましたので、Qシリーズのみで構成したところはMELSECNET/H、一部AnUSシリーズを使用したところはMELSECNET /10を使用しました。そこから現場に分散したCC−LINKに接続しています。
CC−LINKはデジタルIO、アナログIO、タッチパネル、デジタル調節計などに接続されています。
タッチパネルはCC−LINK割付で4局占有でまかなえるものはCC−LINK、それ以上に必要なものはRS−422で接続しています。
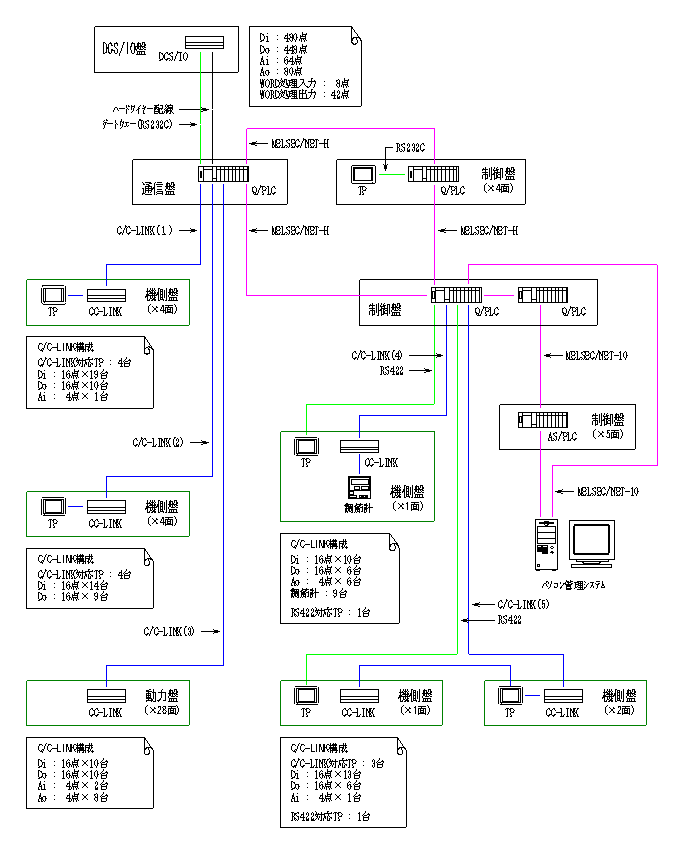
この例ではCENTUMとハードワイヤー取合はOMRONのIOリレーを使用して絶縁しましたが、設備的にも金額的にもメリットの少ない方法です。
今回施工したのは三菱電機製QシリーズとEthernet接続し、この シーケンサをマスターとしMELSECNET10(既設シーケンサがQシリーズでないため)で各シーケンサと接続する方法です。
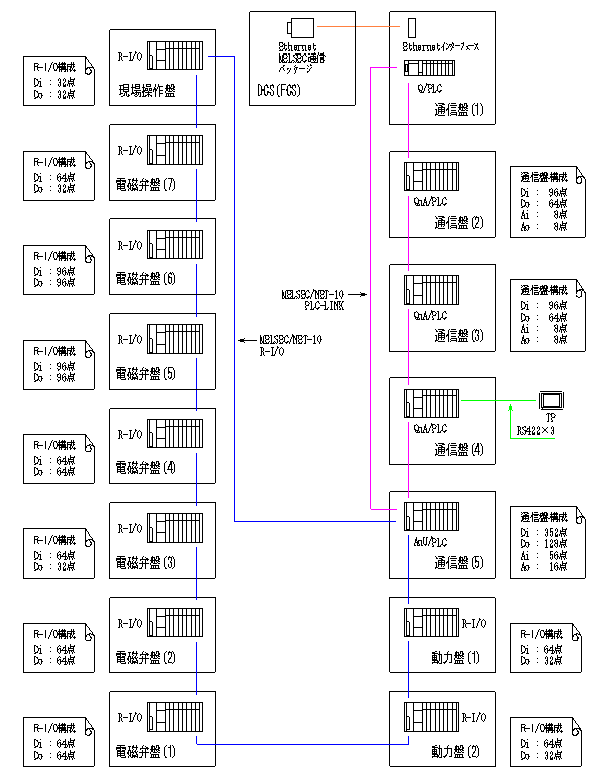
通信盤とはPLCリンクで接続し、電磁弁盤等機側の盤とはR−I/Oで接続しています。この構成は既設の構成を出来る限り変更せずに、DCSと接続ためにNETを2系統に分けました。
EXとの接続
上位に日立製作所DCS/EXを使用した接続例 です。EXの場合はMELSECNET/10専用ボードを持っていますので、ハードワイヤー取合やゲートウエー取合をする必要がありません。PLC−NETの一部のように扱えますので非常に便利です。
NET−10構成,CC−LINK構成共にかなり高負荷の状態ですが、前もって机上でテスト出来ますので実際の対置上げにはそれほどの時間は掛かりません。
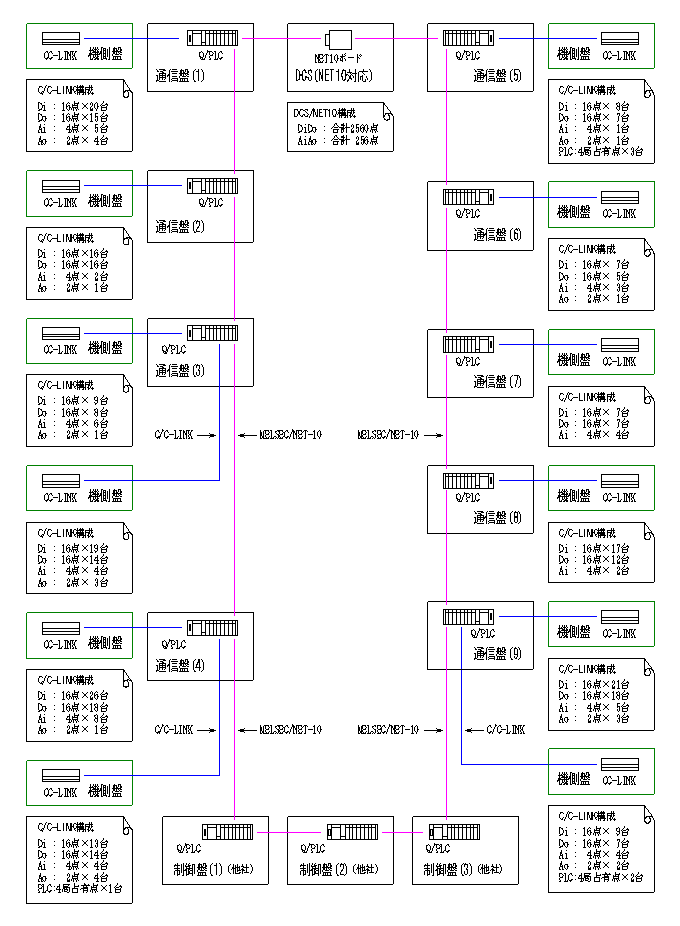
今後、更に変わった構成がありましたらご紹介致します。

マンマシンインターフェースにタッチパネルは欠かせない状況になってきました。工場全体のデータを確認できるよう、39台のタッチパネルを要所に置いた例をご紹介します。台数が多いのでマルチリンク接続をしています。
合計28台のシーケンサをMELSECNET /10で接続し、更に199台のシーケンサを10系列のMELSECNET /10で接続、そのデータの一部をハードワイヤ接続で2台の通信用シーケンサに取り込みました。メインとなる通信盤PLCはQシリーズに更新済みなのですが、ネット上の全てのPLCがQシリーズに更新されていませんので、未だにNET/10を使用しています。
タッチパネルは総計39台を11系列のRS422でマルチリンク接続しています。
RS422の1系列あたり最大4台のタッチパネルですが、さすがに応答が遅くなります。不要なデータエリアを削除し、操作優先モードで使用しています。今、これと同じ台数のタッチパネルを使うならEther−Netを使用します。
尚、使用したタッチパネルはデジタル製のGP577シリーズですが、さすがに最近故障が発生し始め、GP3000シリーズに更新しています。GP3000シリーズも最近はマルチリンク対応になりましたので通信上の置き換えは問題ないのですが、将来的にはEthernetに通信変更したいと考えています。
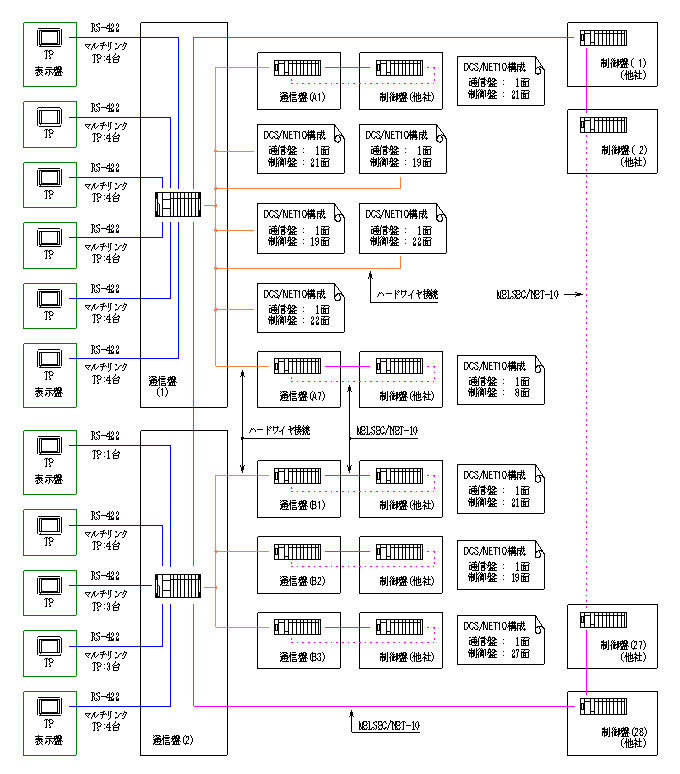

下水道や農村集落排水中のBOD、SSなどの除去を有効に行わせるため、循環水路の活性汚泥混合液に空気中の酸素を溶解させると共に、攪拌に必要な流速を確保する設備をオキシデーションディッチ用曝気装置と云います。この曝気装置制御のマンマシンインターフェースにタッチパネルを使用し、全ての設定、制御が画面上で出来るようなシステムをご紹介します。
外観
外観はアルミプレートにタッチパネルを組み込んだ形になっています。裏面にはシーケンサやワンループコントローラーが内蔵されています。これで全てを制御しています。
なお、現在の機種は外観は黒色梨地塗装に変更し、落ち着いた雰囲気にしました。
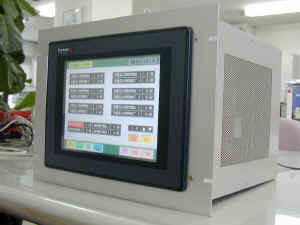
運転モード選択画面
運転モードとしては処理量の少ないときに使用する「初期モード」と定常時の「タイマーモード」「DOモード」「併用モード」が選択可能です。更に「DOモード」以外は2台ある攪拌機の主となる1号攪拌機の他に2号攪拌機に対して「連動T」「連動U」「単独」のモードが選択可能です。
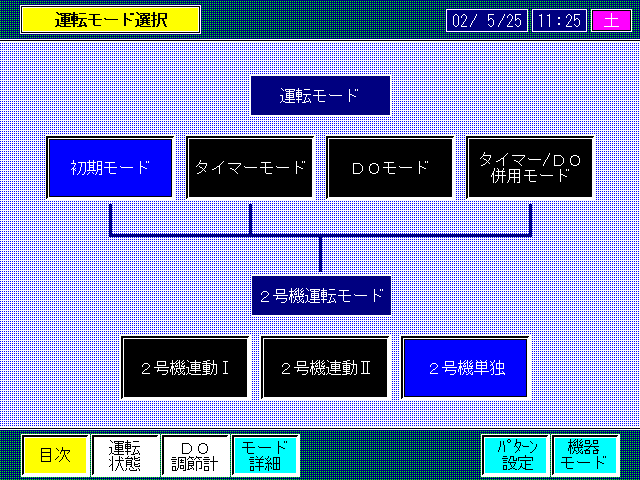
運転状態表示画面
運転状態をグラフィック的に表示します。一般的にはこの画面で管理できます。現在選択している運転モードはランプ表示され、各攪拌機の回転数は円グラフ表示、また現在の運転状況が「高速」「低速」「DO制御」などでランプ表示されます。
攪拌機の運転状態は停止で緑、運転で赤、また高速で早く回転、低速でゆっくり回転するように表示されます。同時に流れ方向に矢印が移動して行きます。
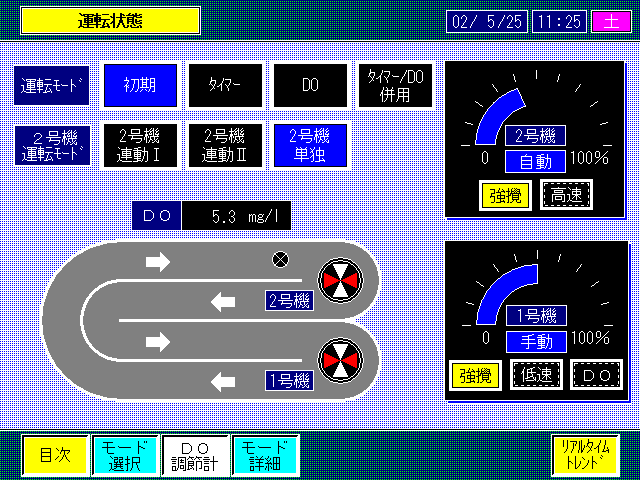
運転時刻設定画面
運転モードに従って一日の運転開始時間などを設定表示します。「初期モード」の場合は攪拌機運転開始時刻を設定します。▲にタッチすれば15分ごとに時刻が進み、▼にタッチすれば逆に遅れていきます。この例では曝気開始10に19:30を設定しています。最大24点の運転開始時刻が設定できます。4パターン設定できます。
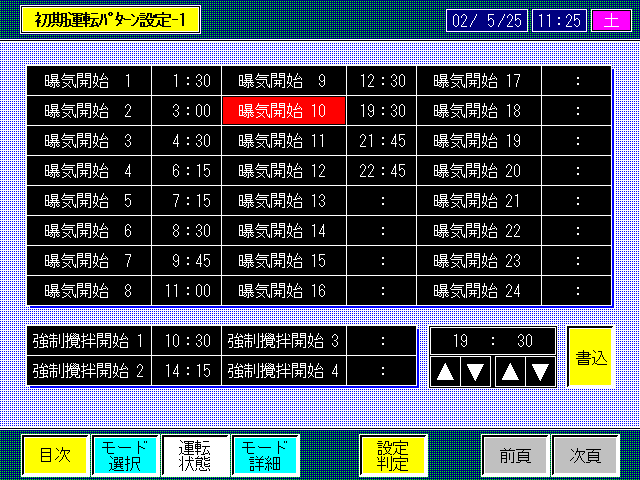
定常運転時のパターンは多量流入時間帯を設定し、「タイマーモード」「DOモード」「併用モード」で運転方法が異なります。最大6点の多量流入時間帯が設定できます。4パターン設定できます。
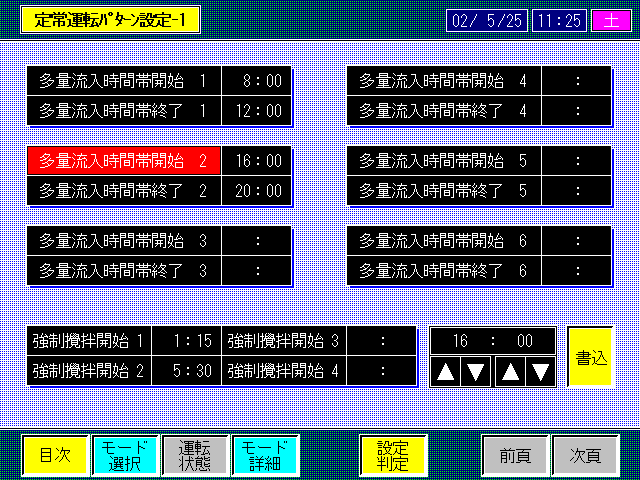
曜日別運転パターン設定画面
運転モードに従って一日の運転開始時間などを設定しても、曜日などによって処理量が変わることが考えられます。そのため前述の各運転時刻設定画面は4パターンずつ設定することができ、曜日毎にそのパターンを設定することが可能です。
今週の土曜日が終了すると次週パターンが今週に移動します。次週の日曜日に「設定無」(無表示)が設定してあると土曜日が終了しても今週のパターンを続けます。
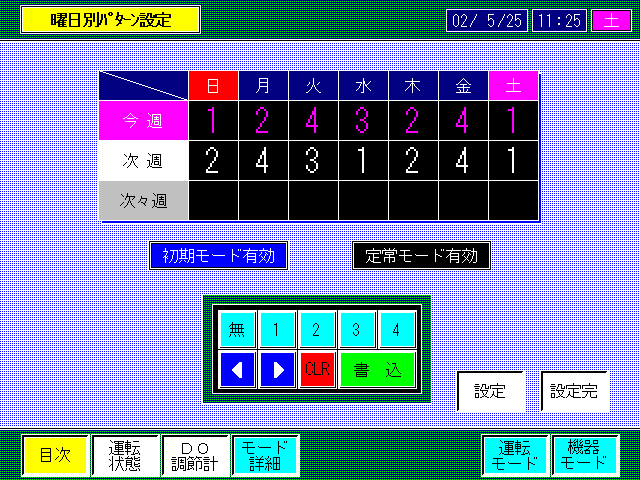
DO調節計画面
「DOモード」のときは、DO調節計を使用します。表はタッチパネルのみですから、画面で調節計の必要部分を表示、操作します。
同時に「DOモード」に関連する設定もこの画面で行います。
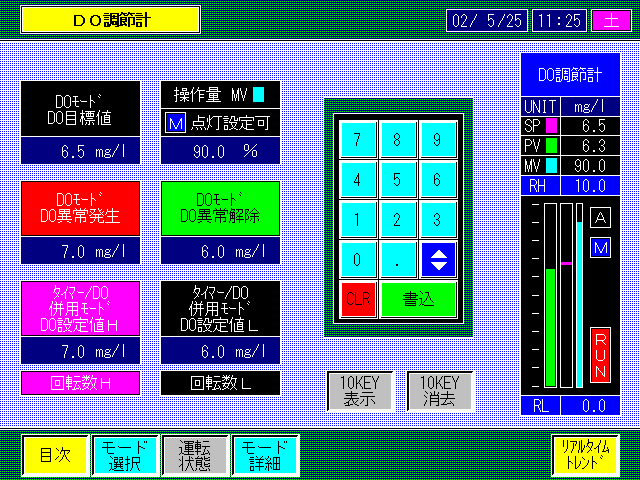
タイマー設定画面
各運転パターンの細かい時間設定を行います。タイマー番号にタッチするとその内容説明画面がウインドウ表示されます。ここで項目で使われている色が次の詳細パターン説明に関連します。

詳細パターン説明画面
各運転パターンの時間設定値と各攪拌機などがどの様に連動するかを詳細に説明する画面です。前述のタイマー設定画面で設定した値が反映されます。「初期モード」「タイマーモード」「DOモード」「」併用モード」の4パターン画面があります。
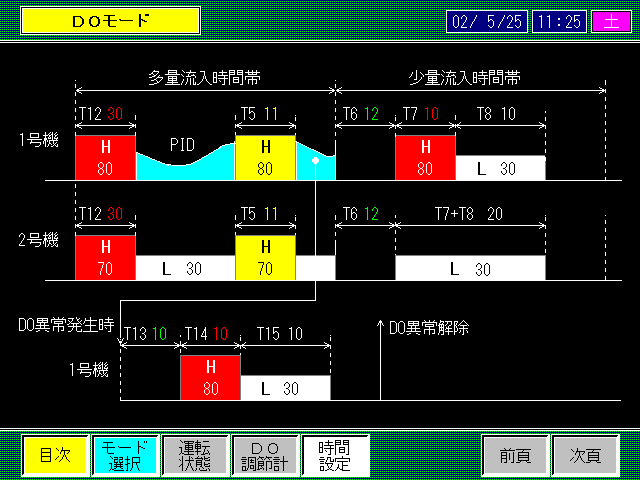
その他にも色々な画面があります。定常時に開けておく画面、必要時に設定する画面、メンテナンスのときのみ使用する画面などがあります。どの様な処理も基本的に全てタッチパネルの画面だけでできるようになっています。操作も簡単ですので、大いに活用できるシステムだと思っています。
なお、現在の機種はタッチパネル画面配色もモノトーンに変更し、落ち着いた雰囲気に変更しています。

精製糖工場の真空結晶缶は精製糖プラントの中でもっとも中心となる部分です。輸入原糖をろ過器や活性炭吸着塔、イオン交換樹脂塔などを通して精製し、精製された糖液を真空結晶缶でバッチ処理して結晶化し、遠心分離機で結晶を分離、乾燥冷却し製品とします。
一言で砂糖と言っても種類は非常に多く、例えばほぼ同じ品質でも結晶の大きさが違うものなどがあります。皆さんよくご存じの双目糖などはいい例です。その製品毎に結晶化するレシピが準備されます。したがって結晶缶の自動制御は膨大なデータ処理が必要になってきます。
結晶缶の工程
結晶缶はバッチ処理します。それを煎糖といいます。もっとも標準的な煎糖工程は次のようになります。
「排気」 缶内を真空にします。
「吸込」 ある液面まで糖液を吸い込みます。
「濃縮」 カランドリアと呼ばれる部分に蒸気を注入して糖液を濃縮していきます。
「起晶」 缶内の糖液が過飽和の状態になったときに、シードと呼ばれる砂糖の種を吸い込ませます。
「育晶」 吸い込んだ種を元に砂糖の結晶を成長させていきます。糖種により育晶方法が変わります。
「仕上」 結晶の大きさなどを確認して終了の準備に入ります。
「煎締」 結晶の成長の最終工程です。
「落糖」 真空ブレークし、結晶と糖液の混ざった液を結晶缶から排出します。
「洗缶」 結晶缶内を蒸気、温水などで洗います。
「休止」 全て終了し、次のバッチ処理を待ちます。
実際には双目糖などは「落糖」工程で全て排出せずに一部残し、次のバッチでその結晶を元にさらに大きく成長させる分缶(カッティング)などの技術もあります。
結晶缶の測定データ
真空結晶缶では測定データとして缶内真空度、濃縮するために使用する蒸気の流量、結晶缶に供給する糖液流量、結晶を成長させる途中で使用する差水(さしみず)流量、結晶の大きさを間接的に測定する固さ計、結晶缶内の糖液液面計などがあげられます。さらに糖液の過飽和度を真空度と温度から演算します。
これらのデータを工程毎に、製品毎に制御していきます。そのデータがレシピです。
固さ計は缶内に回転翼を挿入してその負荷を測定する方法や、攪拌機の消費電力から演算する方法などがあります。
12糖種のレシピ機能
今回納入する真空結晶缶では12糖種を煎糖します。各工程毎にそのレシピがありますが、さらに育晶工程では10〜12工程に細分化されます。
その細分化された工程のなかで糖液を使用した糖煎、差水を使用した水煎、両者を使用した糖水煎、真空度を変化させる空気煎などが設定されます。さらにそれらの繰り返し回数、繰り返す毎に加算減算させる固さや液面の偏差を設定するなど膨大なデータがレシピとして記憶されます。
機器構成
今回の真空結晶缶自動制御には、レシピ設定と状態表示用にタッチパネル(デジタル製)、工程制御とレシピ処理にシーケンサ(三菱電機製)、アナログ制御と過飽和度演算などにワンループコントローラ(エム-システム技研製)を使用しています。これらはお互いにRS232Cで接続されています。
制御盤はこんなにシンプル
かっては幅1〜1.2mくらいの中通路を設けたような大きな制御盤でしたが、今回は内部を裏表の2層構造にしさらに扉の裏面も使用した幅600mmの既設盤のリプレースでした。従いまして盤寸法は全く同じにし、そのまま入れ替え可能としました。盤面、盤内がいかにシンプルになっているか比較して見てください。
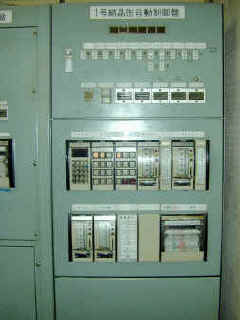
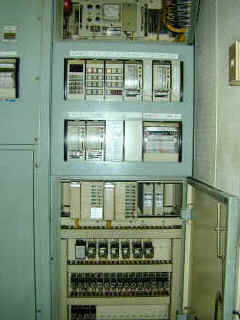
既設盤は表面が上下3分割で中央部が計器、上段が表面が自動弁SWや糖種選択デジSW、積算計など、内部は固さ計変換器ユニットなどが、下段内部にリレーユニットが実装されています。裏面内部には計器変換器が並んでいます。
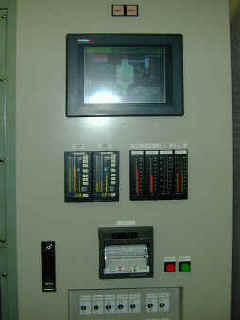
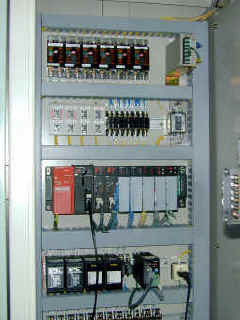
今回の制御盤は盤面上部からタッチパネル、ワンループコントローラーおよび指示計、記録計、自動弁SWが実装されています。盤内は上段が固さ計変換器ユニットが、後はシーケンサ、計器変換器、リレーユニットなどです。裏面はありません。
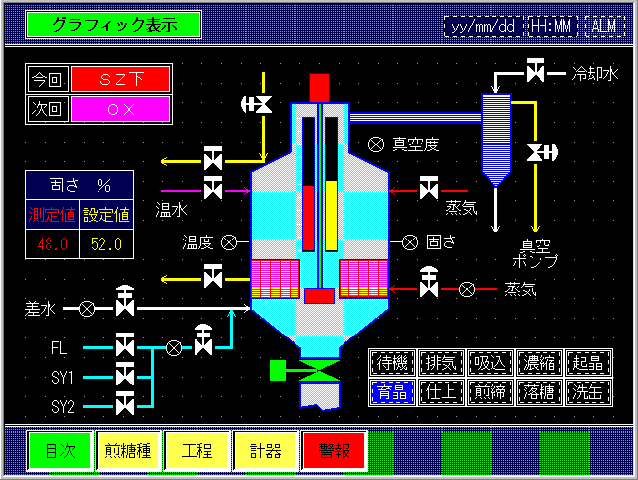
タッチパネルのグラフィック図です。実際の画面では弁の開で色が赤に変わります。煎糖終了で次回煎糖表示が今回煎糖表示に移ります。ディスチャージ弁は半開で桃色、全開で赤色に変わります。硬さは設定値と測定値をデジタル表示すると同時にバーグラフ表示しています。次回、差水弁を使用するときは差水調節弁が、糖液弁を使用するときは糖液調節弁が点滅して知らせます。

ワンループコントローラーの演算機能を使用した非線形比例制御を使用した液面制御の例を紹介します。結構簡単な制御なのですが効果はかなりあります。
制御の目的・方法
次のような装置があります。プロセス1は例えば半連続操作を行っていて、周期的に受槽流入液が増減したり、停止したりする場合、受槽の液滞留容量を変化させてプロセス2に送る流量を平均化させる操作が必要になります。
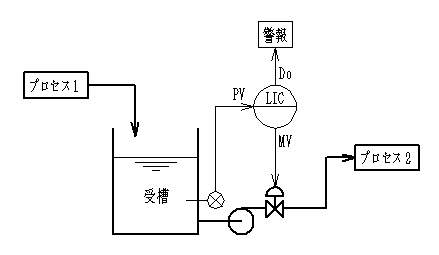
そのために受槽の液面設定値からある幅にバッファー領域を設け、液面の変化に対する調節弁の動作を緩やかにする範囲を設けます。バッファー領域を越えた受槽の上限近くでは急激に調節弁を開いてオーバーフローを防ぎ、下限近くでは調節弁を閉じてポンプの空引きを防止します。
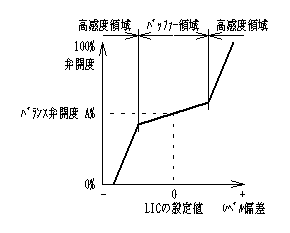
液面設定点(SV)、SVと測定値(PV)が一致したとき(偏差DV=0)のバランス弁開度(A%)、バッファー領域の幅、バファー領域の感度(K2)、高感度領域の感度(K1,K3)などの設定が必要です。
専門的になりますがこれをワンループコントロラーで実現するには、偏差を取り出し非線形演算ブロックを通し、出力補償に接続します。出力補償の形態は調節計のPID動作を使用しませんので出力補償値のみを使用する置換型に設定します。
設定値の変更
液面設定値(SV)を変更した場合のバッファー領域の移動などを図で説明しますと次のようになります。
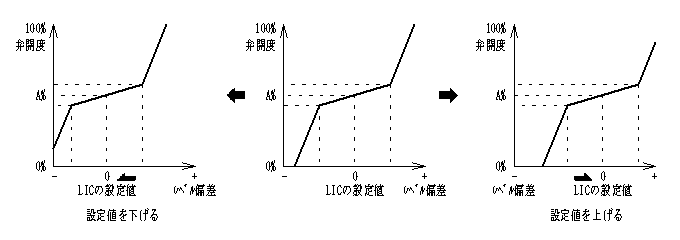
バランス弁開度の変更
バランス弁開度は偏差(DV)=0のときの弁開度です。これは平均流量に見合った弁開度を設定しなければなりません。この制御の最大のポイント点です。出来るだけ定常時に液面変化のない弁開度を探します。
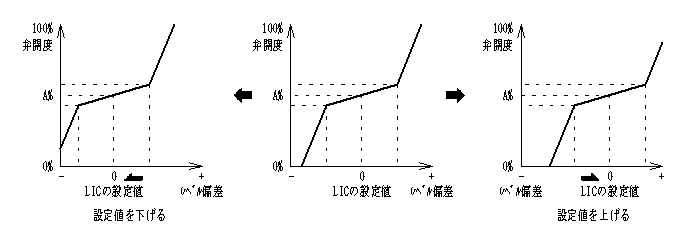
バッファー領域の幅の変更
バッファー領域の幅は設定点から偏差で上下に何%を領域にするかという設定になります。
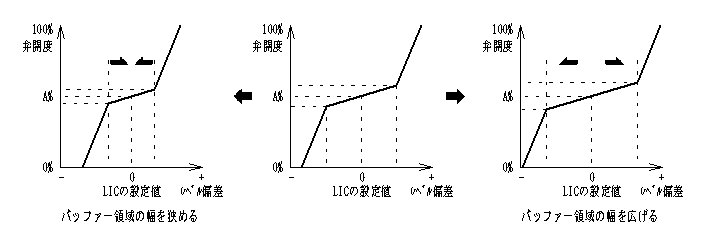
バッファー領域の感度(K2)
バッファー領域の感度は偏差(DV=設定値ー測定値)に対してどの程度応答するかという設定になります。したがって感度(K2)=1のときは偏差がそのまま調節弁への出力(MV)になり、バッファーとしてではなく比例帯100%のときの比例動作と同じになります。ということはバッファーとして使用するためにはK2は1より小さい値でなければいけません。
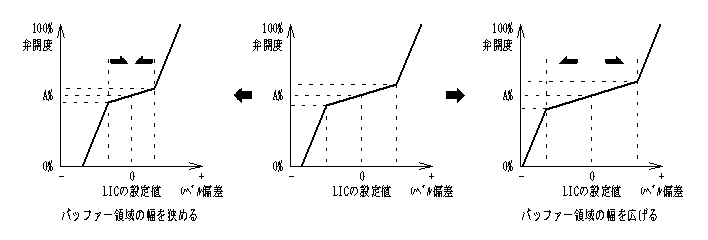
高感度領域の感度(K1,K3)
高感度領域の感度もバッファー領域と同じく偏差に対してどの程度応答するかという設定になります。したがって感度(K1、K3)=1のときは偏差がそのまま調節弁への出力(MV)になり、高感度としてではなく比例帯100%のときの比例動作と同じになります。バッファー領域で感度を落とした分、高感度領域では感度を上げてオーバーフローと空引きを防止しなければいけませんのでK1,K3の設定は1より大きい値にしなければいけません。
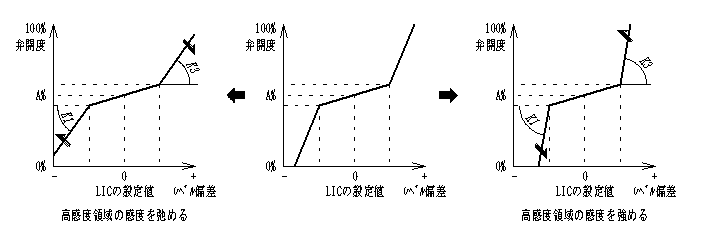
非線形PID制御との違いは
非線形比例制御と非線形PID動作はどこが違うのでしょうか。
非線形比例制御は感度を変えて結果的に比例帯を変えた様になりますが、実際はPID機能は全く使用しません。偏差に対して出力は常に同じ値になります。
非線形PID動作はバッファー領域は設けますがそのバッファー領域もPID制御は働きます。積分動作がありますからバッファー領域でも偏差があればやがてそれをカバーするように出力が変化します。ここが最大の相違点です。この制御は中和点近くのpH制御によく利用されます。
バランス弁開度設定値はどの様に見つける?
この制御の最大のポイント点であるバランス弁開度は偏差が無いのときの弁開度ですが、これは平均流量に見合った弁開度を設定しなければなりません。ところが平均流量が時間で変化するようであれば、この開度も平均流量に見合った開度を時間とともに変化させればより安定する事がわかります。全体の流量バランスから算出してこの開度を変更できるように出来ればベストといえます。
一般的にはもっとも平均的な流量のときに液面変化が少ない弁開度を設定します。
更に、プロセス2の状況により同一弁開度でも流量は変化します。ということはこの出力を流量制御にカスケードするというのもより安定化させるための一つの方法です。
機会があれば設計にそれほど時間のかかる制御ではありませんので試してみて下さい。

このWebサイトに関する質問やコメントについては
をお送りください。